Comment construit-on un bâtiment en pièces détachées ?
Presque un an que je travaille chez DS-Elcobyg, une entreprise danoise produisant des éléments préfabriqués en béton armé pour la construction.
Le Danemark construit beaucoup en éléments prefabriqués en béton armé. Hasard au pays de Lego ? je ne crois pas. C’est pas forcement super parce qu’il faut une perceuse à béton pour le moindre truc, mais ça a quand même de nombreux avantages.
NB : Les videos disponibles dans cet article sont partagées sur mon instance peertube. De ce fait, elles ne peuvent être lues que sur les navigateurs les plus aboutis, tels que Firefox ou Chrome.
Un processus industriel
On a beau produire pour la construction, on reste quand même plus proches d’un processus industriel. Nos tolérances sont aussi bien plus prôches de tolérances industrielles que de tolérances chantier. Par exemple les tolérances pour les dimensions externes d’un élément sont de +/- 4 mm. Un niveau de précision qu’on ne peut garantir sur un chantier. Il est également bien plus facile de garantir la position des armatures dans le béton sur une table de coffrage qu’au fond d’une banche.
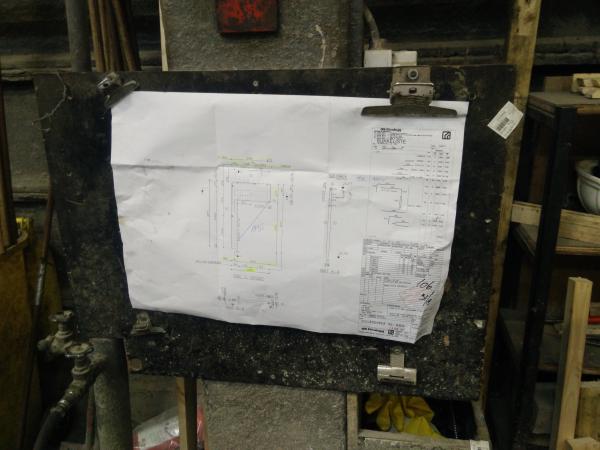
Un plan pour un élément (que j’ai dessiné).
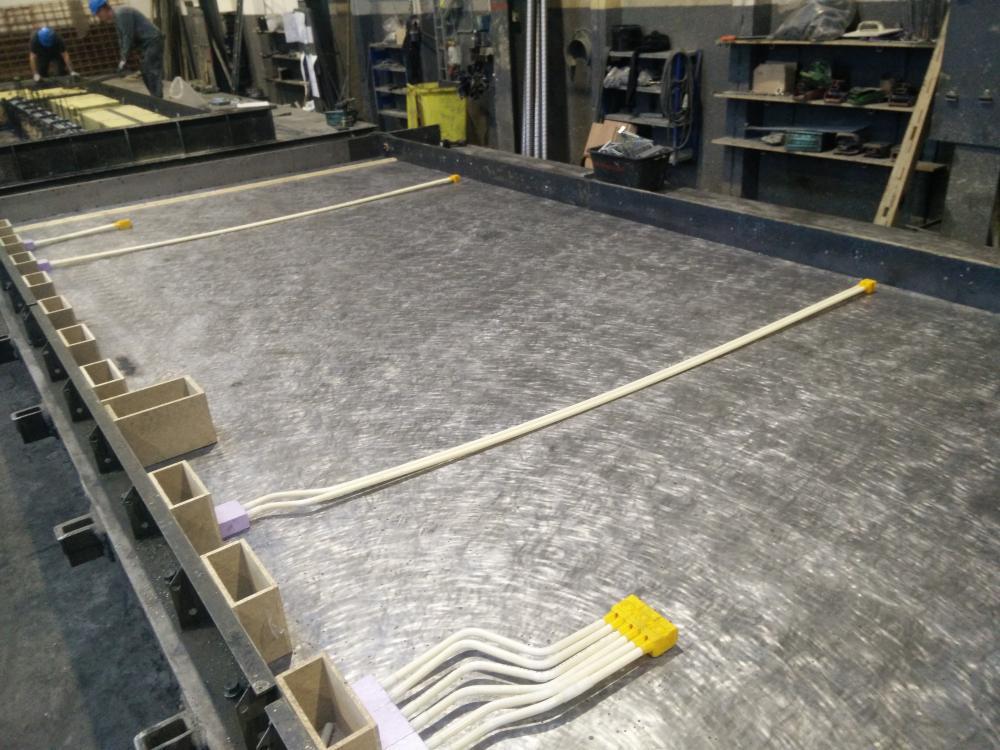
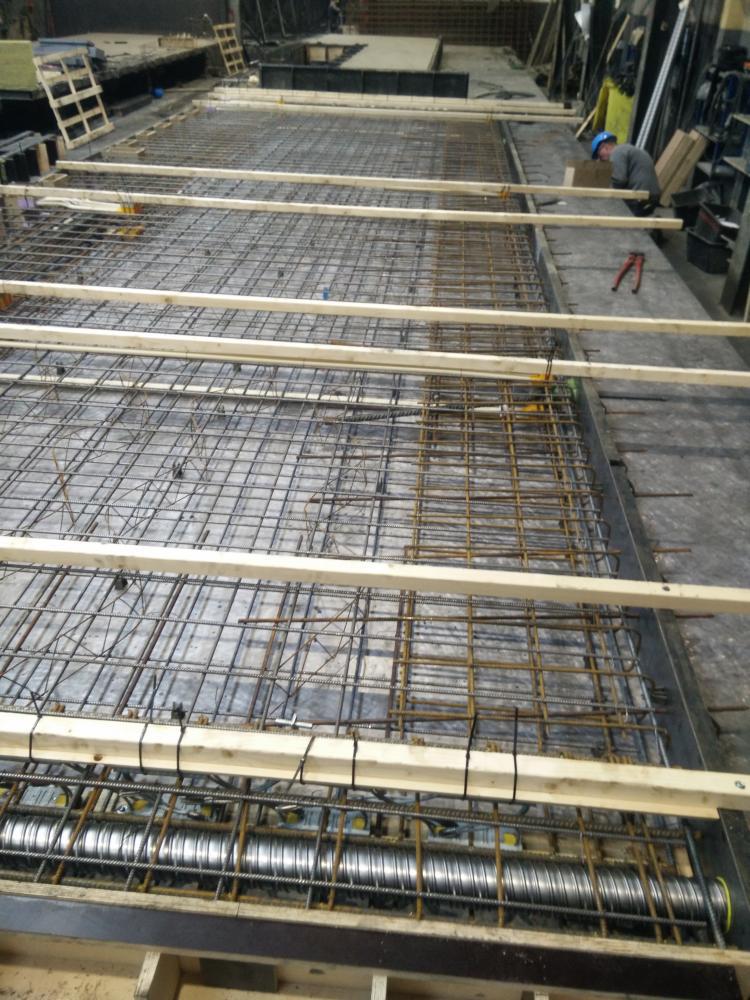
Un des élements que j’ai déssiné, en cours de fabrication. La video en dessous montre le debut du coulage.
Fin du coulage d’un élément.
On a donc notammant importé des pratiques de l’industrie, pratiques qu’on a du mal à appliquer sur un chantier conventionnel. Par exemple un contrôle qualité des éléments finis.
Une culture de la sécurité aussi. Non pas que l’usine soit un paradis sûr où l’on pourrait lâcher des bébés à peine nés, on utilise quand même du materiel lourd. Mais il est quand même moins dangereux de tomber d’une table de coffrage de 50 cm de haut, que d’une banche de 10 mètres. Ca reste quand même moins dangereux que sur un chantier classique.
Nous pouvons utiliser des bétons spéciaux ou fabriquer nos propres treillis d’armatures !
Notre machine à treillis soudés.
Ce processus industriel permet donc d’obtenir des éléments de bâtiment de meilleure qualité esthétique. Le design danois (et scandinave de manière plus large) est minimaliste et les architectes aiment utiliser du béton brut. Les murs de façades peuvent également venir avec leur parement et leur isolation intégrée.
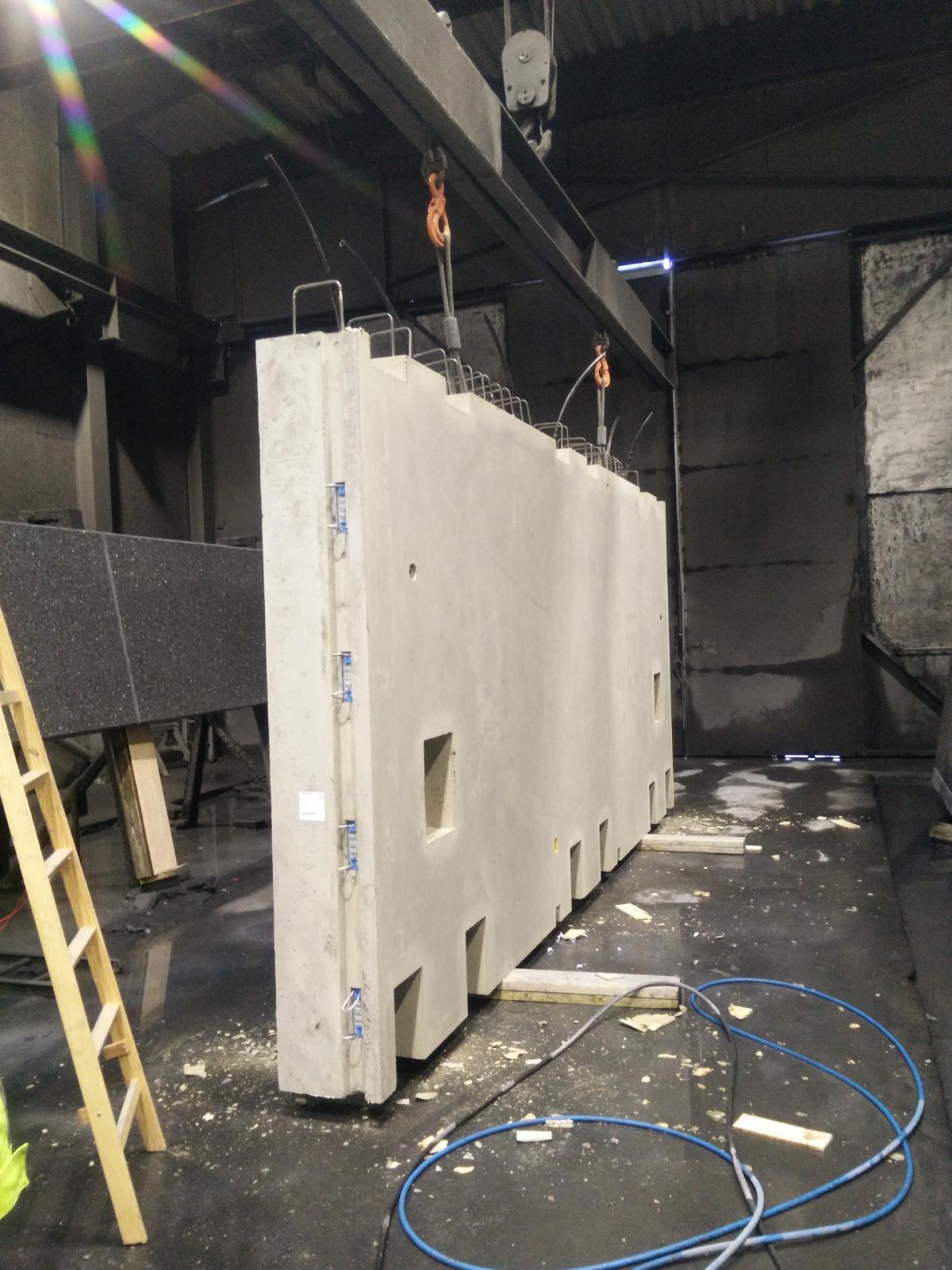
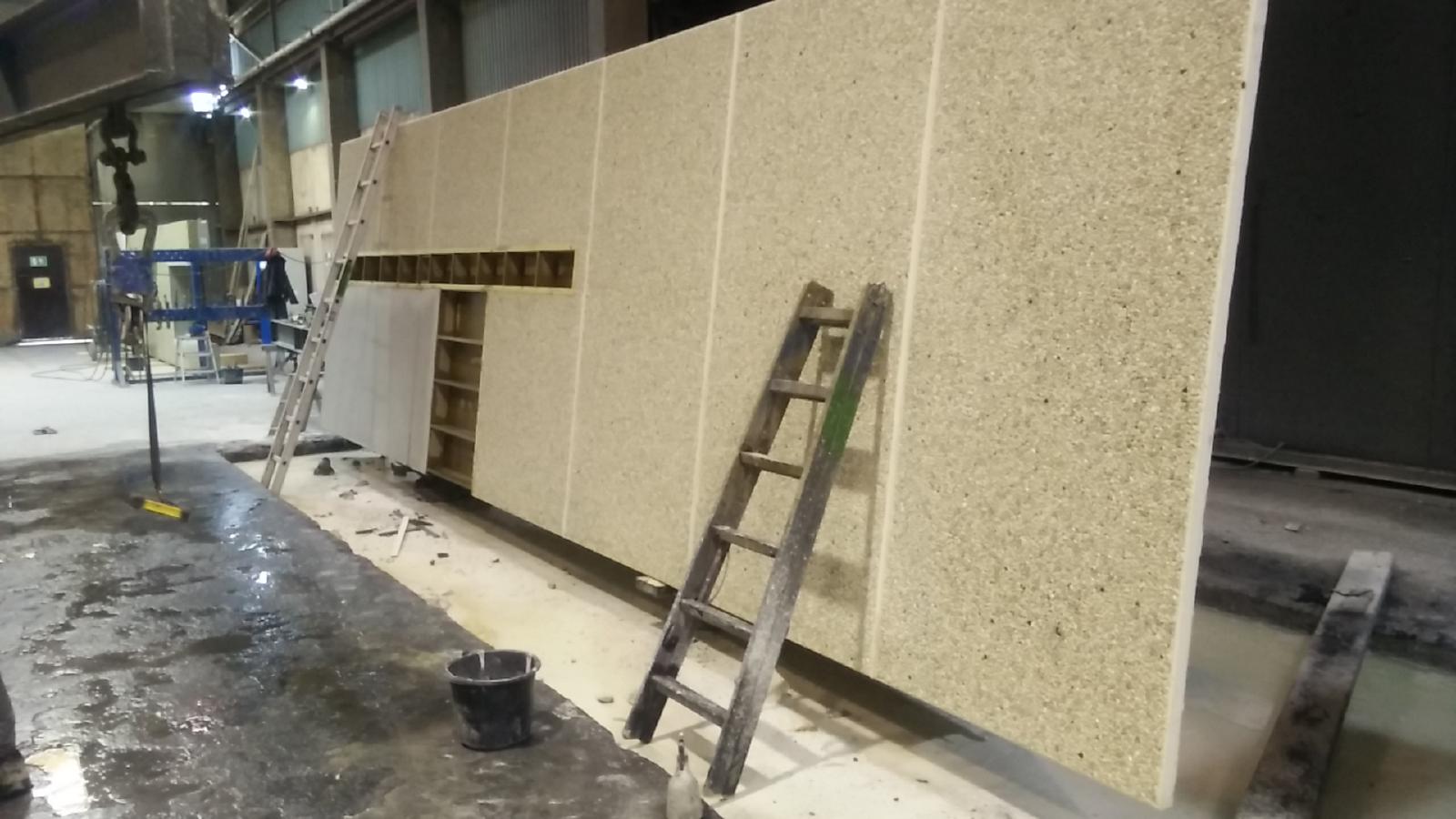
Élément avec parement intégré
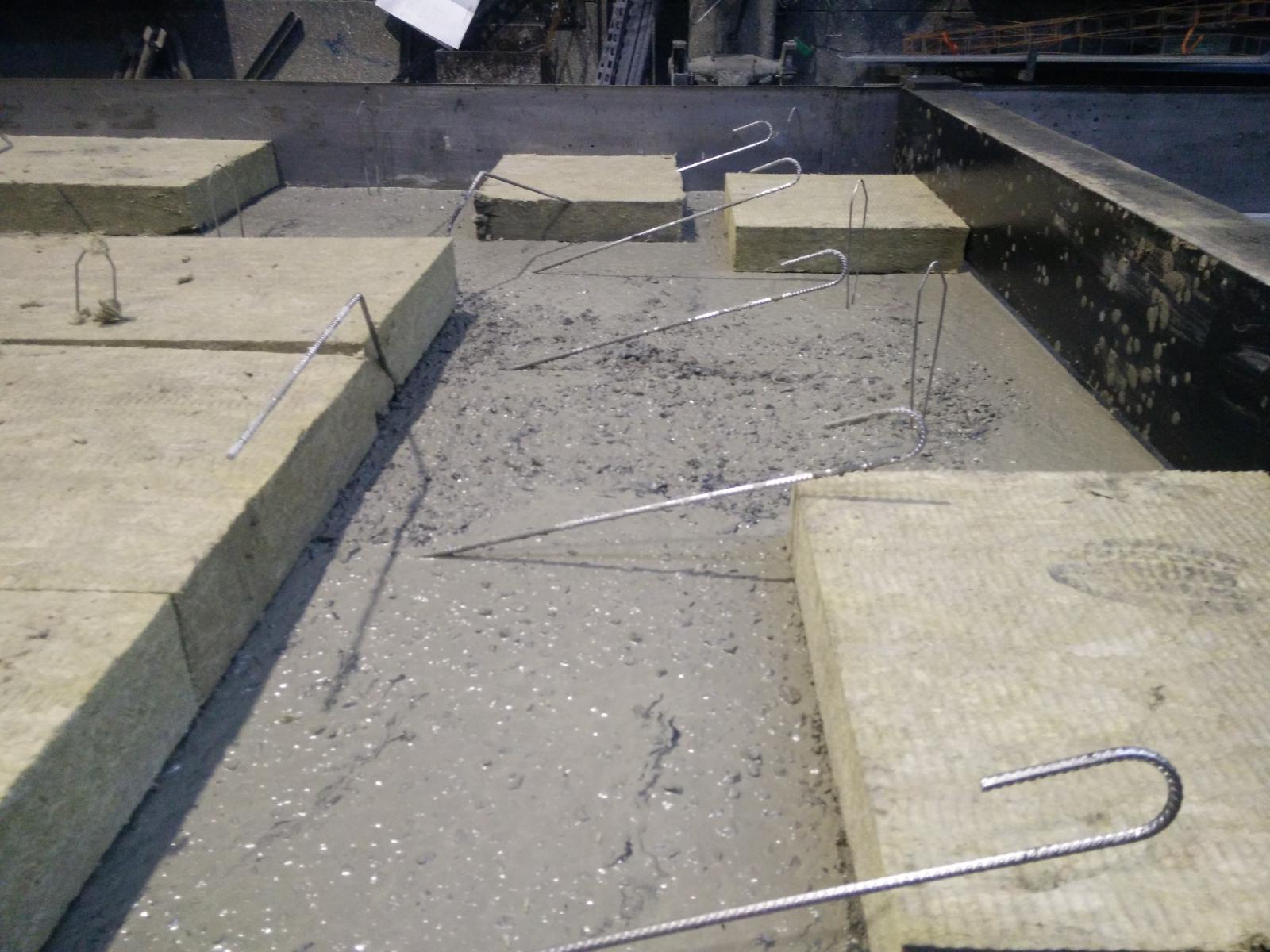
Élement-sandwich en cours de fabrication. On coule d’abord la couche de parement, faiblement armée. Au bout d’une demi-heure, on peut poser l’isolation, sur laquelle on va couler l’élément porteur. Les deux parties beton sont liées par les armatures de liaison coulées dans le parement.
Logistique
La logistique devient une partie importante des opérations lorsqu’on construit un bâtiment de plusieurs centaines de tonnes à 100 km de sa position finale.
Ainsi, il faut integrer le coût des transports dans les prix, organiser ces mêmes transports, integrer aussi leurs contraintes dans nos processus industriels. Les dimensions maximales des éléments viennent pour partie des tailles maximales autorisées des camions.
Les pièces sortent aussi toutes belles de l’usine, mais il n’est pas dit qu’elles arrivent dans le même état sur le chantier.
Il faut organiser, planifier les coulages. Ceci occupe, chez nous, une personne à temps plein, et elle intervient à toutes les étapes du processus de fabrication, du moment où on commence à diviser le bâtiment en éléments individuels, jusqu’à la coordination des livraisons avec le monteur final.
Diviser pour mieux regner ?
La divsion du futur bâtiment en éléments modulaire a ses avantages… Mais aussi ses inconvénients ! On s’est en effet débarrassé de tout l’aspect “artisanal” d’un chantier classique et des problèmes inhérents. Mais soudainement, on voit apparaître d’autres problèmes, qu’on a pour ainsi dire crée nous-mêmes.
La logistique impose des dimensions maximales sur route, mais nos propres installations ont aussi leurs contraintes.
- on a des dimensions maximales, correspondant aux tables de coffrage de l’usine.
- on a aussi des poids maximums, correspondant en fait aux capacités de levage maximum des ponts roulants de l’usine, qui doivent approcher les vingts tonnes.
Ceci determine les dimensions maximales des éléments. Ces dimensions doivent aussi correspondre aux contraintes propres du projet et à sa structure.
Si on peut couler plusieurs éléments de dimension moyenne à la fois, les éléments les plus longs et les plus massifs ne peuvent être coulés que sur des tables spécifiques, donc également un seul à la fois. Tout ceci requiert beaucoup d’organisation de la part du chef de production et de la responsable logistique.
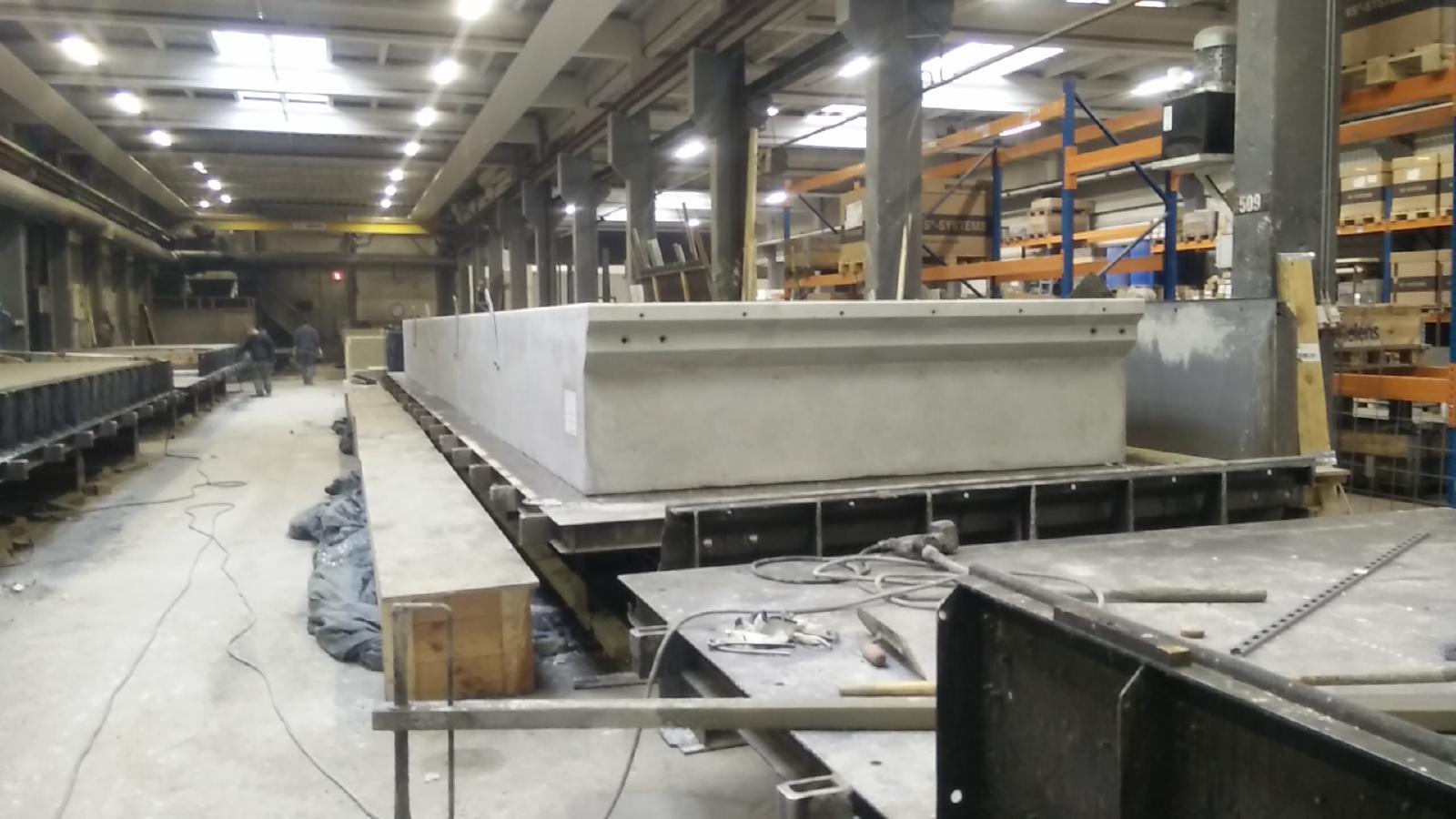
Un élément de grandes dimensions.
La division en éléments fait aussi facilement perdre la vue d’ensemble du bâtiment. On peut facilement oublier que cet élement ne sera pas qu’une plaque de béton. Il sera aussi un élément porteur (ou non) et ses armatures doivent être calculées suivant ses contraintes maximales.
Au cours du dessin, on a facilement tendance à faire une armature en panier, qui va bien contenir le béton. On pense plus difficilement aux descentes de charges finales et aux armatures necessaires pour ca.
Ce découpage en éléments individuels impose également tout d’un coup, dans l’élement, l’utilisation d’inclusions necessaires justes pour ça :
- ancres de levages et leurs armatures (qui ne seront utilisées que quelques jours sur la durée de vie totale de l’élement).
- armatures et/ou dispositifs de liaison.
Tout ça occupe de la place dans le béton, place qu’il faut calculer et qui entre souvent en conflit avec d’autres inclusions (armatures, isolation, reservations pour passage de conduits d’áeration, etc). Voire, place qu’on a parfois… pas !
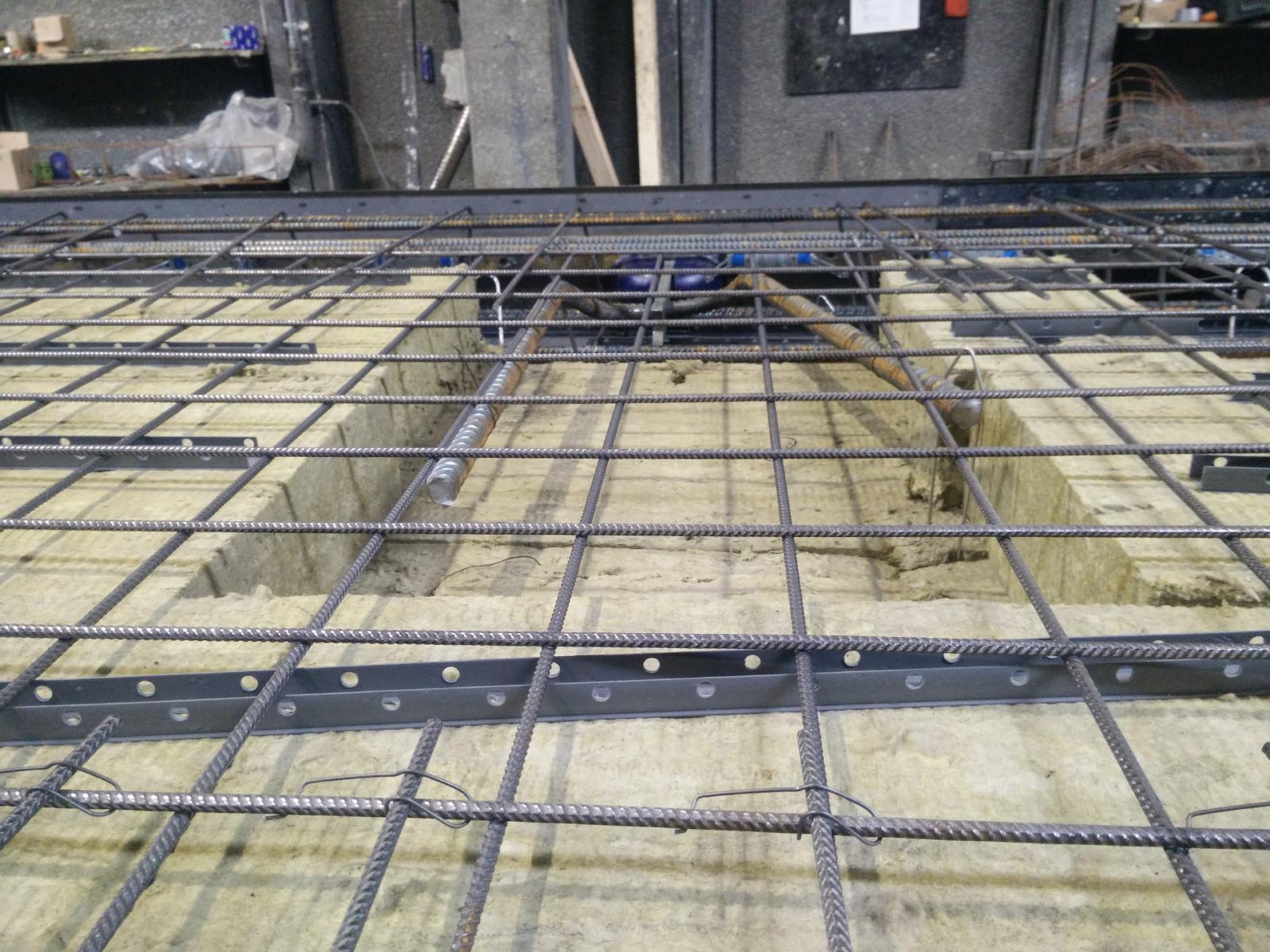
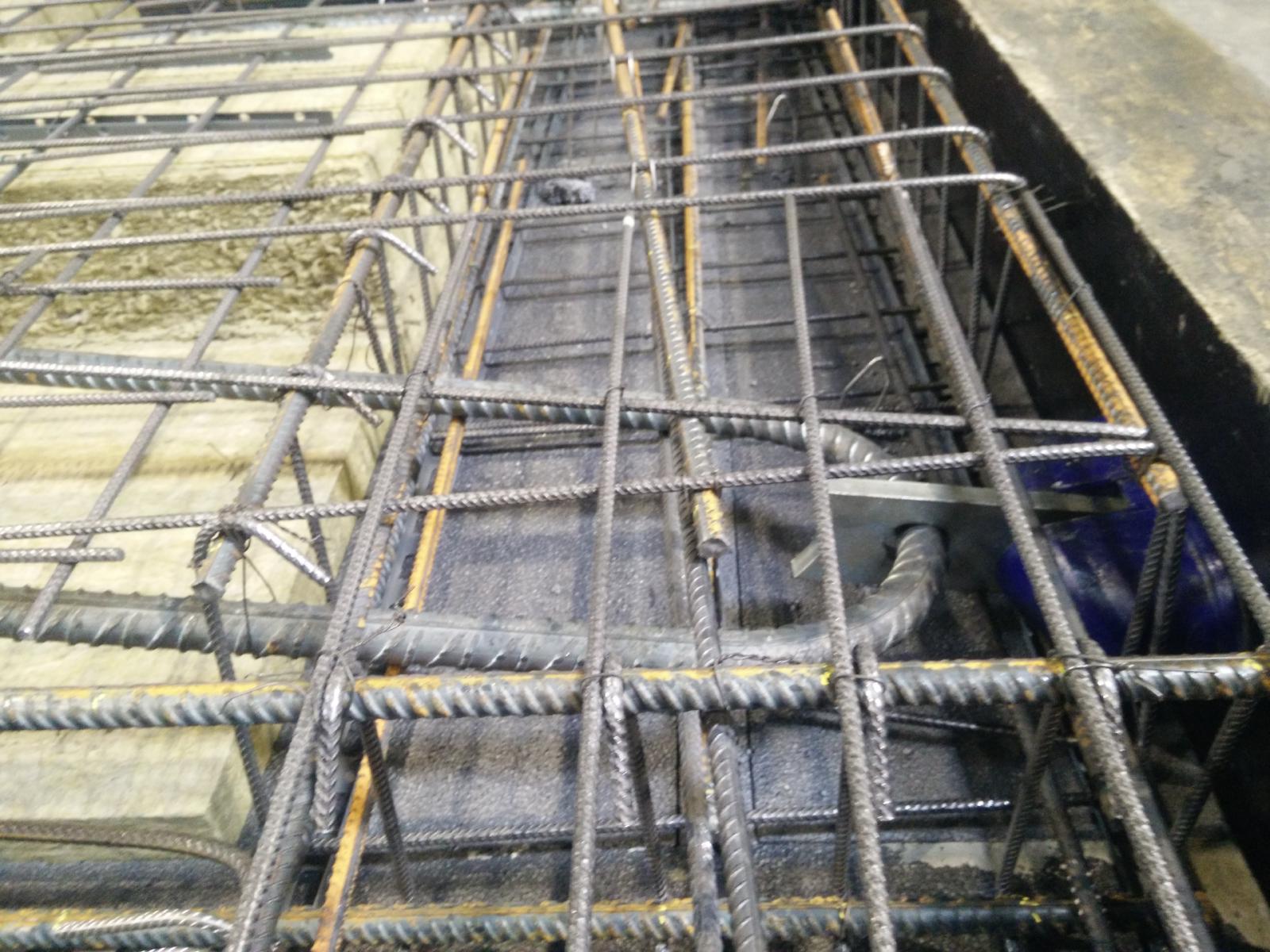
Ici, on a dû découper dans l’isolation pour permettre le passage des ancres de levage.
Une rigueur necessaire.
L’utilisation d’éléments préfabriqués s’avère aussi plus rapide, mais elle impose d’avoir les plans finis et cohérents bien plus tôt.
Lorsqu’on coule sur place, in-situ, on peut s’adapter quasiment jusqu’au dernier moment. Avec des éléments préfabriqués, il faut au contraire être très rigoureux. Si on a un élement juste 1 cm trop long, ça peut causer des soucis. Et on peut facilement se retrouver à jouer au sudoku : la modififaction d’un élement peut très bien imposer d’importantes modifications sur plusieurs autres éléments, par des effets de dominos.
Avec de la préfabrication, on peut aussi multiplier les intervenants. Poteaux, poutres, dalles, voiles et refends… Chacun peut être produit par une entreprise differente ! On peut aussi couler le bâtiment dans l’ordre qui nous interesse le plus : couler un élément du 10ème étage avant un mur du rez-de-chaussée. Ceci peut toutefois s’avèrer une arme à double tranchant.
NB : Toutes les photos et vidéos ont été enregistrées avec le téléphone de l’auteur, sur le lieu même de production. De ce fait, comme des travailleurs ainsi que l’entreprise sont invoqués, photos et vidéos sont placées sous licence CC BY-NC-SA.